Pempek’s One Button Ex Auto Roof Bolting System.
Together Pempek's Ebox and HMI is a unique electronic control system package for controlling, monitoring, and automating roof drilling/ bolting rigs used in gaseous underground mining environments.
They are designed for easy installation into new and existing mobile mining machinery. The system is composed of a drill rig-mounted, flameproof, electric over hydraulic control module and a companion flameproof push-button Human-Machine Interface user control station.
The Ebox module can be readily adapted to suit roof drill rig models from several different manufacturers.
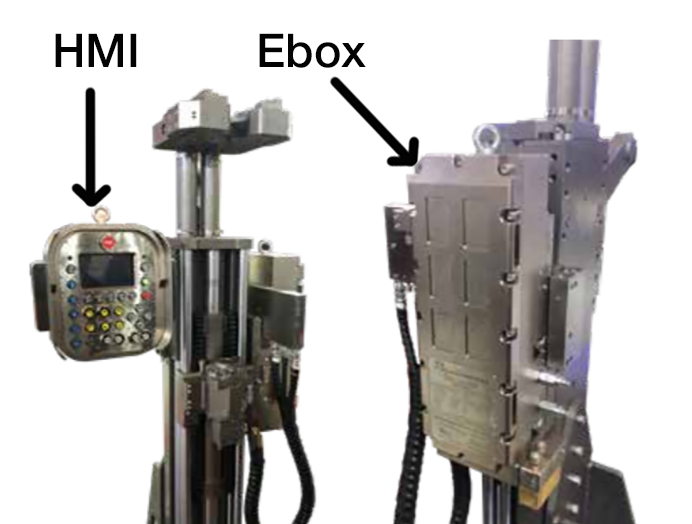
Key Features & Benefits
Pempek Automation provides maximum productivity.
Just one control cable from PLC to HMI.
Just one control cable from HMI to Ebox.
Massive reduction in Hydraulic hosing.
Reduction in labour time for drill rigs assembly on machine.
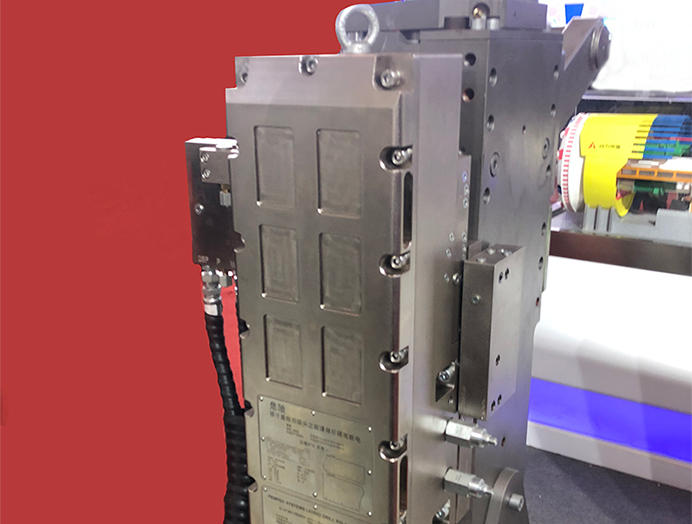
Why Ebox?
Drill rigs for mobile mining platforms are typically constructed from hydraulic cylinders, hydraulic motors, and actuators. Traditionally, a large set of hydraulic hoses is connected between the body of the drill rig and a hydraulic switching valve bank. The valves controlling flow to the drill rig functions are then either controlled by hand levers or by a remotely located control system.
The EBox combines direct control hydraulic valves, solenoids, sensors, and electronics into a single, flameproof-certified package. The unit attaches directly to the mast of the drill rig – via a hydraulic adaptor plate. This cleaner assembly does away with up to 30 hoses; depending on the make and model of the drill rig. Some hydraulic hoses are still required to provide fluid power to the drill rig.
The EBox module also connects to the drill head unit of the drill rig.
The HMI Control Station is a flameproof-certified operator panel complete with function push buttons and an integrated graphics display. A simple power and data cable connect the HMI station to the EBox. The operator uses the HMI station to control and monitor all drilling and bolting functions.
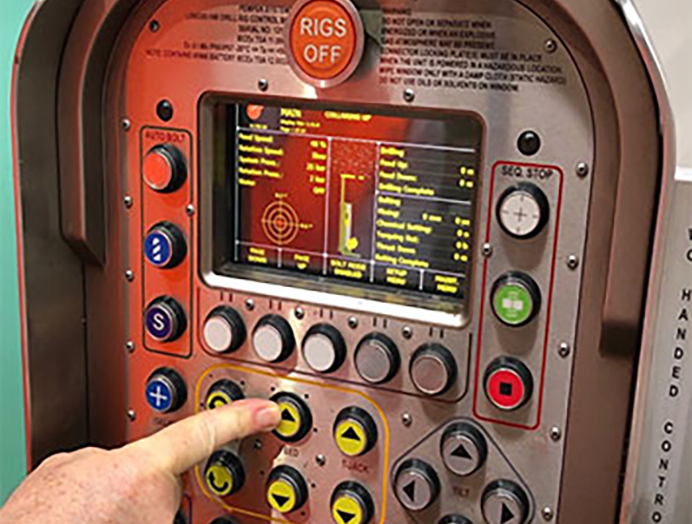
Improved Operator Safety
The roof drilling system significantly improves the comfort and safety of mineworkers in three ways:
Reduction of hand and arm strain injuries.
Prevention of unplanned rig movement by monitoring hydraulic spool position.
(i.e. stopped hydraulic valve spool)
Roof Strata Mapping (predict roof weakness).
Drill rig parts can move rapidly, driven by electric and hydraulic motors and actuators. Physical damage or system failure can cause the machine movements to occur without warning.
A so-called unplanned movement places operators at risk of serious injury or death. The Pempek drill rig control system mitigates the risk of unplanned drill rig movement events by implementing a design that is consistent with IEC61508 (International standard for functional safety of programmable systems). Safety features have been designed into the product to greatly reduce the likelihood of an unplanned movement due to electronic failure and also to shut down the hydraulic power source (pump) if an unplanned hydraulic movement is detected.
Two-hands operation for functions which potentially could cause a hazard for the operator. Reducing injuries caused by hands being pinched or caught on moving parts whilst the drill rig is tilting.
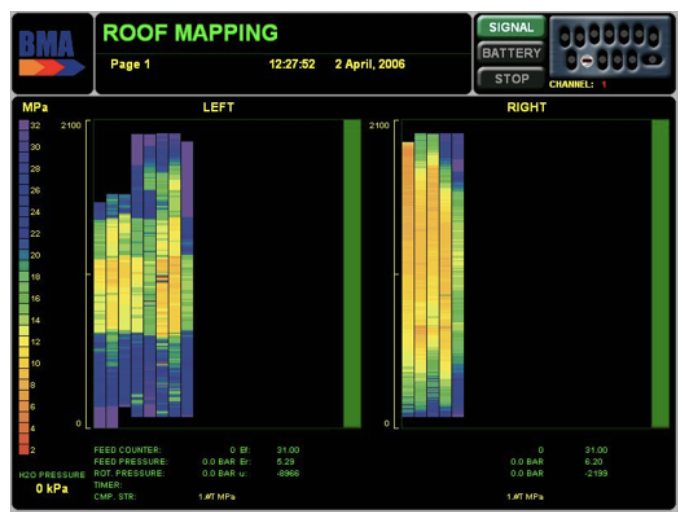
Roof Strata Mapping
Roof bolting is a technique used by mine engineers to prevent roof falls in underground mining. Based on studies of the geology, engineering staff make decisions about the best way to support the roof and prevent tunnel collapse. This translates into a specific plan for bolting patterns and other roof support strategies.
Although roof control has developed into a reliable and precise science, accidents can and do still occur when the roof geology changes unexpectedly. This typically requires the addition of more bolts or other measures to ensure that a roof fall does not occur.
The Pempek drill rig control system measures roof strata hardness distribution while drilling each bolting hole. The system collates measurements to construct a spectrographic roof map of strata hardness.
The map indicates the hardness of the roof strata at varying drilling depths using a colour-coded scale. The map appears on the main screen of the HMI so workers can quickly assess the roof conditions at any time.
This information quickly reveals if the roof is weak and additional bolting or support is required. The system can also generate an alarm to alert mine personnel of unstable roof conditions that could result in an imminent roof fall.
Productivity
The increasing use of electronic control and automation has enabled enormous productivity gains across many industries.
The Pempek drill rig control system provides a similar advantage in drilling and bolting productivity through push button control and automated features.
The system empowers operators to achieve drilling and bolting cycle times up to 15% faster than with previous technology.
Data Logging
With drilling and bolting functions of the drill rigs under the control of an intelligent, computer-controlled system; all drilling, roof mapping, and maintenance data is continuously logged. Pempek has several methods by which the data can be retrieved from the machine and used for reporting and analysis.
Monitoring for each drill rig's total drilled distance and number of bolts installed can alert mine management about the scheduled time for drill rig maintenance.
Maintenance
Pempek drill rig control system features fewer parts, cables and hydraulic hoses when compared to a traditional approach. This automatically translates into lower cost for installation as well as reduced maintenance requirements.
By integrating all hydraulic and electronic control functions into one system, a very advanced level of diagnostic monitoring is possible.
Pempek roof drilling system is the perfect solution for mobile mining equipment where roof drilling and bolting is required.
Example Application
A common application is roof drilling rigs on a bolter miner. The bolter miner combines a continuous drum-type miner with continuous semi-automatic roof drilling and bolting. The platform provides rapid roadway development with a single machine; replacing the traditional concept of two machines – a miner and a separate mobile bolter platform.
The simplicity of the system allows it to be easily integrated into a new machine during manufacture, or into an existing machine – at the time of overhaul.
The system also provides options for different drilling and bolting systems. For example, a high-pressure water management module can be added to the machine in order to provide pressurized bolt grout flow for self-drilling bolts (such as the HILTI “one-step” system).
PEMPEK’s One Button Ex Auto Roof Bolting System can be added to the existing Control System on the bolter-miner machine or be configured to run as a stand-alone system requiring only:
- Information if Bolt Mode is active thus allowing to operate roof bolter functions.
- STOP output from HMI module to integrate into machine STOP circuitry.